Bosch Common Rail Injector Repair Manual
2) Insert injector (do not touch the nozzle tip) and sliding clamp with clamp bolt. 3) Fit Injector pipe (Nuts finger tight only) 4) Injector clamp bolt (torque: 2.7±0.2 kgm). If injector too loose, cylinder may loose pressure,. If Injector too tight, may result in pinching of the needle, resulting in knocking or misfire.
- Bosch Common Rail Injector Repair Manual Diagram
- Bosch Common Rail Injector Repair Manual Tool
- Bosch Common Rail Injector Repair Manual Transmission
Transitioning from working on the old-school conventional (mechanical) diesel fuel injection systems to the modern, computerized High-Pressure Common-Rail (HPCR) fuel system requires a change in thinking and a change in diagnostic procedures.
We’ve all heard the phrase ‘you can’t teach an old dog new tricks’ but we’re going to smarten you up by offering you our 5 tips to ensure the old diesel dogs out there can still perform a few new tricks.
Tip 1: Do not Pinch or Restrict the Fuel Return Line
Savvy pump tuners know that the early Bosch fuel pumps (‘VE’ pumps, and ‘P’ pumps) can be tricked into increasing the injection pressure by restricting the return fuel flow. One could get away with this type of ‘modification’ due to the style of pump, and the lower pressures that these pumps were limited to.
This same trick cannot be applied to the HPCR systems.
If you have an engine with an HPCR fuel system and you attempt to restrict the fuel flow of the CP3 pump, the pump will build up so much housing pressure that it will actually blow the driveshaft seals and inspection plugs right out of the pump! The CP3 pump depends heavily on the fuel return line to relieve the excess fuel pressure that is being built up inside the pump and send it back to the tank.
Again, DO NOT restrict the return fuel line when performing diagnostic checks, and in some cases (with modified CP3 pumps) you will actually need to INCREASE the size of the return line to handle the additional flow.
Tip 2: Do Not Over-pressurize the Fuel Inlet
We all love making money and going on holidays – the more the better. More is not always better when it comes to HPCR fuel pressure – too much inlet fuel pressure can create the same type of problems as restricting the return fuel line. There is a ‘multiplication effect’ to the fuel pressure going into the pump – if you feed fuel into the pump at too high a pressure, it will develop tremendous pressure (up to 40,000PSI) and can pop seals, damage the CP3 pump internally, or damage the injectors. If you are running a CP3 in a high-performance application, we highly recommend installing a fuel supply pressure gauge to ensure there is correct fuel pressure at all times.
Recommended feed pressures for CP3 and CP4 equipped engines:
Ford scanner f-super download. ALL the OBD-II vehicle interfaces in a single cable, rugged case. Using the enhanced Ford interface, a typical Ford vehicle will support 200 - 300 sensors within half a dozen systems; that's essential systems such as ABS, airbags, GEM, ICM, etc. Our enhanced Ford interface coverage is only matched by factory tools; we have support for 3,400+ sensors selected from all 58 systems. This is a savings of hundreds of dollars over the competitors' unitsAlthough Ford does implement the largest subset of the OBDII standard, the typical vehicle only supports 20 - 40 sensors and is limited to emissions powertrain.
- Dodge/Cummins ’03 – ’16 (5.9L & 6.7L) no less than 8 PSI / no more than 15 PSI.
- GMC/Duramax ’01 – ’16 (6.6L) no less that 8 PSI / no more than 10 PSI.
- Ford/Powerstroke ’11 – ’16 (6.7L) no less than 8 PSI / no more than 10 PSI.
Tip 3: Minimize Condensation Formation and Water Contamination – Fill ‘er Up!
We all know that Diesel fuel is hygroscopic (it absorbs water). Therefore it is no surprise that the overwhelming #1 reason for diesel fuel system failures: water contamination.
For this reason, if your engine is going to be sitting unused for more than 30 days, we highly recommend filling up fuel tanks completely (to ensure the least amount of air space is available for condensation to collect), and also changing fuel filters more frequently if the engine sits around a lot.
Water (condensation) collects on the walls of the fuel tank creating little moisture droplets that form during the daily heating and cooling of the surrounding air. The greater the temperature differential, the faster the water collects. It usually takes about 28–30 days for condensation to form inside a fuel tank that has not been started. This moisture will accumulate in the fuel and begin to create rust and algae inside the fuel tank, and ultimately contaminate the inside all of the fuel system components.
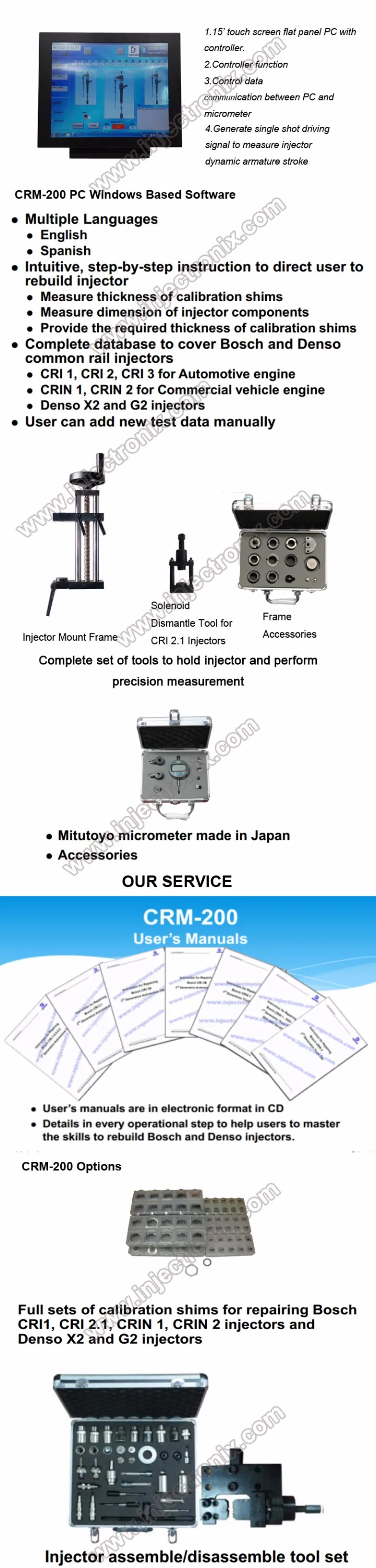
For extended periods of storage, we recommend using Stanadyne Performance Formula diesel fuel additive which contains a fuel stabilizer component, and a mild biocide to extend the life of stored fuel and inhibit algae growth.
Tip 4: Change Fuel Filters Regularly and Improve Filtration.
HPCR injectors are carefully built to exacting standards and are tested multiple times before they even make it into a box to be sold at the counter. If the injector does not pass these rigorous tests, the injector will have to be torn down to start all over again.
Bosch uses the highest quality materials to ensure a long reliable injector life (measuring components to 4 decimal places!) and protecting these very sensitive components from damage, excessive wear or contamination is critical. Purchase Bosch reman parts in our diesel parts store.
There are no additives that can eliminate water from diesel fuel (alcohol-based products or methyl-hydrate products are not for use in diesel fuel), your trusty friend and your first line of defense on your engine is the water-separating fuel filter.
Our suggestion is that you should be changing your fuel filter with every SECOND oil filter change.
One of our complaints about OEM’s is that they install a fuel filter system that meets the absolute bare minimum standards of filtration protection that they can get away with. If you are serious about protecting your investment (and want fewer trips back to the dealer for repairs), improving the fuel filtration system that is on your engine is like buying an extended warranty – your engine and your wallet will be glad you did.
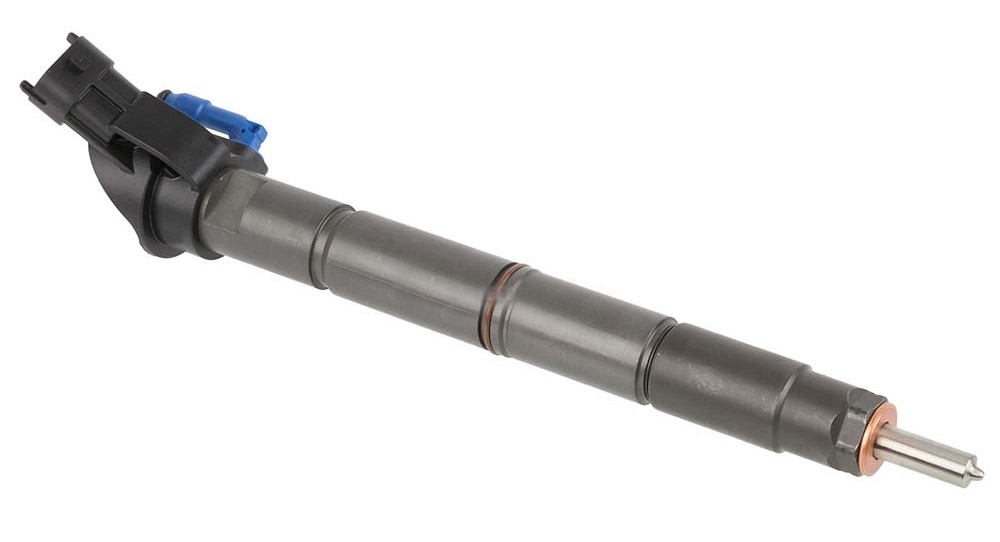
Tip 5: Return Custom-tuned Trucks Back to Stock for Diagnostics.
Custom software tuning for late model trucks has taken the diesel world to a new level of performance and customer expectations. There are many well-engineered products out there that can add tremendous performance and even mileage improvements to your truck, but, in the wrong hands, an untrained person could do some serious damage in a matter of seconds.
Bosch Common Rail Injector Repair Manual Diagram
We highly recommend returning any custom-tuned truck back to its ‘stock’ configuration to improve the accuracy and speed when performing diagnostics. Custom software tunes can ‘mask’ problems and make identifying failing components less obvious, and correctly diagnosing the actual problem more difficult.
Bosch Common Rail Injector Repair Manual Tool
When the software tuning is returned back to stock, the OEM test values and diagnostic check procedures and specifications in the shop manuals will more accurately reflect what is going on, to help you get to the source of the problem more quickly.
Any tuning module added to a healthy, stock truck will make it run stronger – tuning modules should never be used to make up for the lost power on high-mileage / worn-out engines, or to mask complaints of a poorly running engine.
Bosch Common Rail Injector Repair Manual Transmission
While these tips and tricks are certainly not rocket science, it is smart to ensure that the basics are covered when working on modern HPCR fuel systems and that your time and efforts are best spent getting your customers back on the road, and less time chasing your tail.
Some diesel owners buy cheap parts to fix their trucks. Read our blog post on buying cheap fuel injectors and then shop our high quality diesel parts.